Using Building Information Modelling (BIM) to increase quality, reduce errors, and save time.
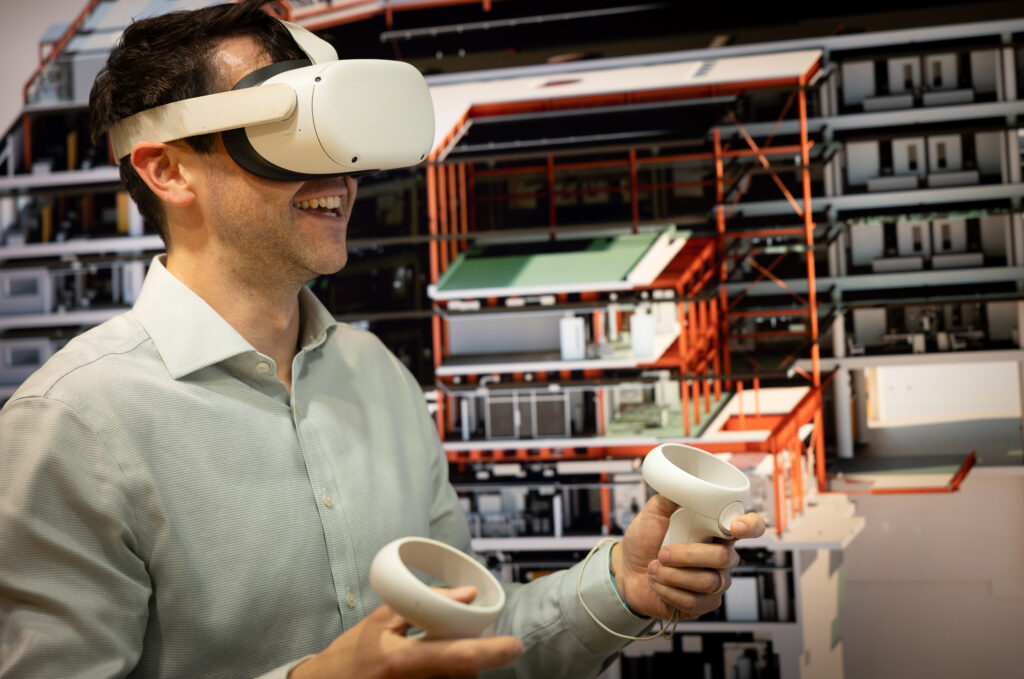
For Bouygues UK, harnessing the capabilities of Building Information Modelling (BIM) technology has been integral to our streamlined construction approach over the past 10 years.
The digitalisation of our industry and the exacting demands of BIM Level 2 have been the drivers for us to look at implementing new ways of working on our projects.
Bouygues UK adopts BIM right from the design phases on the projects we deliver. This involves creating 3D BIM models using various software, primarily for coordination and issue detection among different project disciplines.
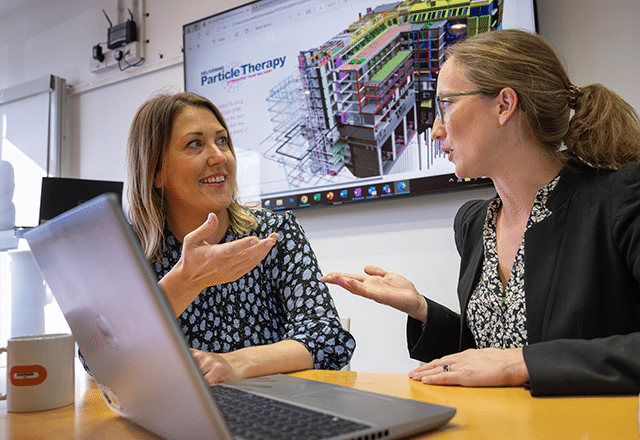
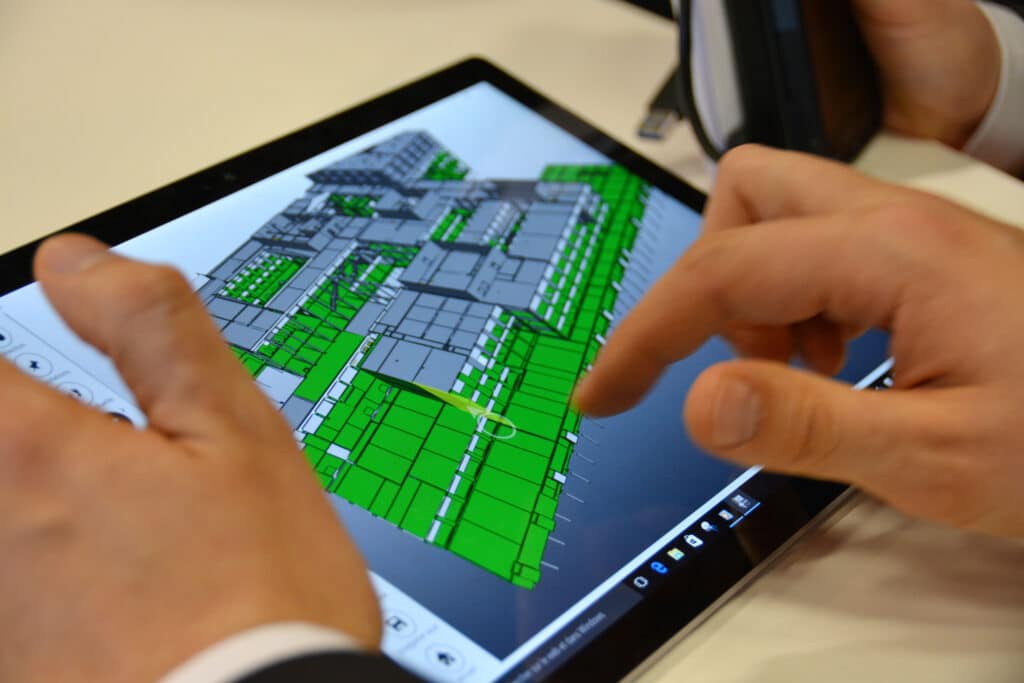
One software that is used by our planning team to incorporate 4D planning is Asta BIM. The software aligns a project’s 3D model to the programme offering the site teams a visual representation of the scheduled works. This software is also used to give quantities of materials so that site teams know the exact amount of material needed to complete their specific tasks.
Asta BIM provides a 3D representation of how the site looks at any time during the project’s lifecycle. The advantages of this software are numerous, from time and resource savings, reduced errors, enhanced collaboration, to a significant reduction in environmental impact due to reduced paper usage. It also ushered in further possibilities for new ways of working and visualisation of site operations.
Case study
Tower Hamlets Town Hall: use of BIM in partnership with Leica Geosystems
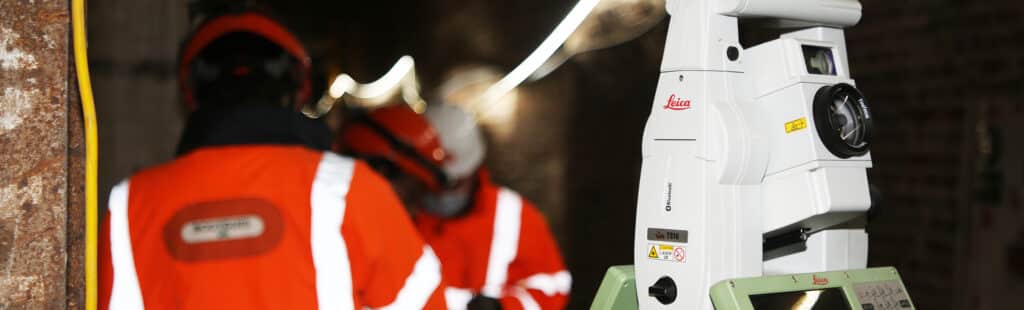
Bouygues UK adopted BIM right from the design phase on the project we delivered for the London Borough of Tower Hamlet, their new Tower Hamlets Town Hall. This involved creating 3D BIM models using various software, primarily for coordination and issue detection among different project disciplines.
As part of our continuous improvement, innovation is key to our business. The digitalization of our industry and the very demanding BIM Level 2 requirements of our Tower Hamlets Town Hall Project have been the drivers for us to look at implementing new ways of working.
Jerome Magnier – Project Director, Bouygues UK
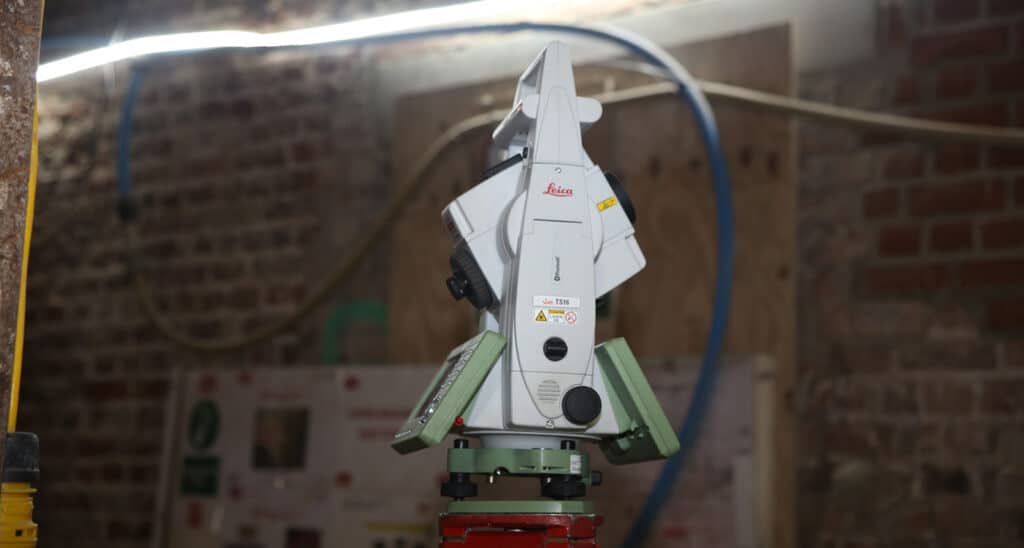
Typically, for large-scale projects, engineers would rely on 2D information generated from BIM models for on-site construction. However, Bouygues UK opted to use the 3D models for site layout and construction, eliminating the need for extensive 2D data.
To achieve this, we partnered with Leica Geosystems to employ their iCON System, which comprised of a robotic total station and specialized software to handle BIM models. The system utilized International Foundation Class (IFC) files, ensuring compatibility with industry-standard software.
With their proposed new technology, Leica were offering the opportunity to bringing the digital BIM model to the construction site and using it on a daily basis during the works. Not only this has helped to streamline a complex process of managing the information but is has helped ensuring the accuracy of the information provided to site, directly extracted from the model. A special contribution to the design and installation work of the MEP in the reconversion of the old Royal London hospital. With our investment in this technology, we increase quality, reduce errors, save time and also contribute to reducing our carbon footprint.
Jerome Magnier – Project Director, Bouygues UK
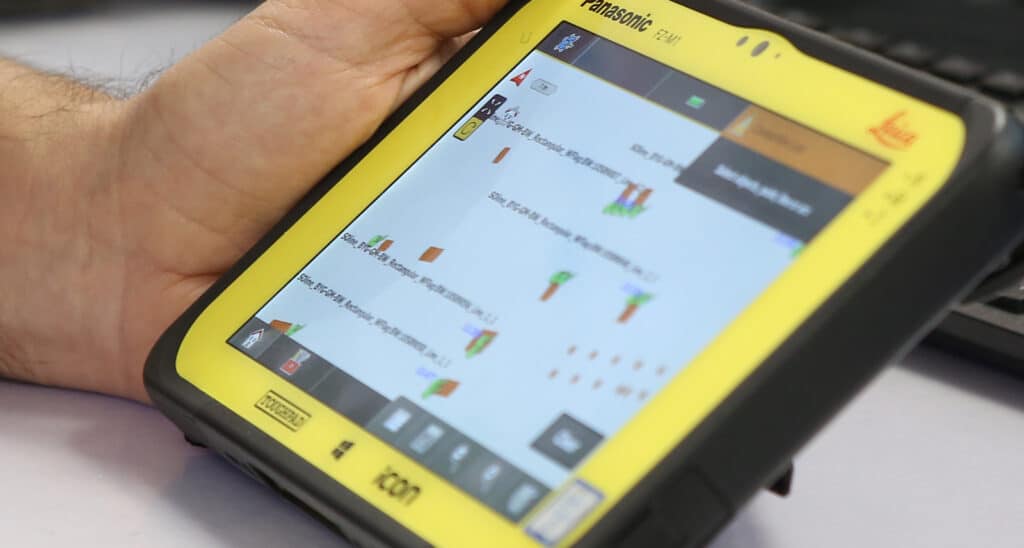
Our BIM Manager at Bouygues UK regularly updated the models in a local folder, making them accessible to all our engineers. Ensuring this was best practice led to enhanced quality control by ensuring the accuracy of the 3D model was consistently cross-referenced with any 2D drawings, maintaining traditional standards.
The iCON system seamlessly connected with the robotic total station, automating the setting out process without the need for 2D data. The system even facilitated setting out on vertical elements, like walls, by calculating intersections with existing structures.
All project-related inquiries, from dimensions to material types, were made directly on the 3D model, making information readily available to the entire project team.
We knew that we wanted to bring the model to the construction site, we knew that the technology was available. So, we looked for and found the Leica iCON system that seemed to meet our expectations. Bouygues UK management decided that Tower Hamlets will be the project to try this approach and after a year of implementation, we can say that the system corresponded in full of what we expected from it at this stage. It was undoubtedly a winning bet
Antonio Santos – Civil Engineering Chief Surveyor, Bouygues UK
The advantages of this approach were numerous, from time and resource savings, reduced errors, enhanced collaboration, to a significant reduction in environmental impact due to reduced paper usage. It also ushered in new possibilities for new ways of working and visualization of site operations.
To be able to receive the latest version of the project from the BIM team and half an hour later, go to the construction site and start implementing works in such a precise way is remarkable. Of course, we worked with our strong BIM department to check the liability of the system to guarantee the quality of the construction. It is not only the time we save but also the decrease in the possibility of making mistakes, and once in the field, you can check your work against the model immediately, do verifications, produce as built and send it back to the office or BIM team. Even our supervisors and team leaders in the site ask to see the system and put questions about the design.
Antonio Santos – Civil Engineering Chief Surveyor, Bouygues UK
In conclusion, Bouygues UK’s integration of BIM models into construction processes demonstrated significant efficiency gains, improved accuracy, and paved the way for closer collaboration between design and construction teams, setting a new standard for the industry.
You might be interested in…
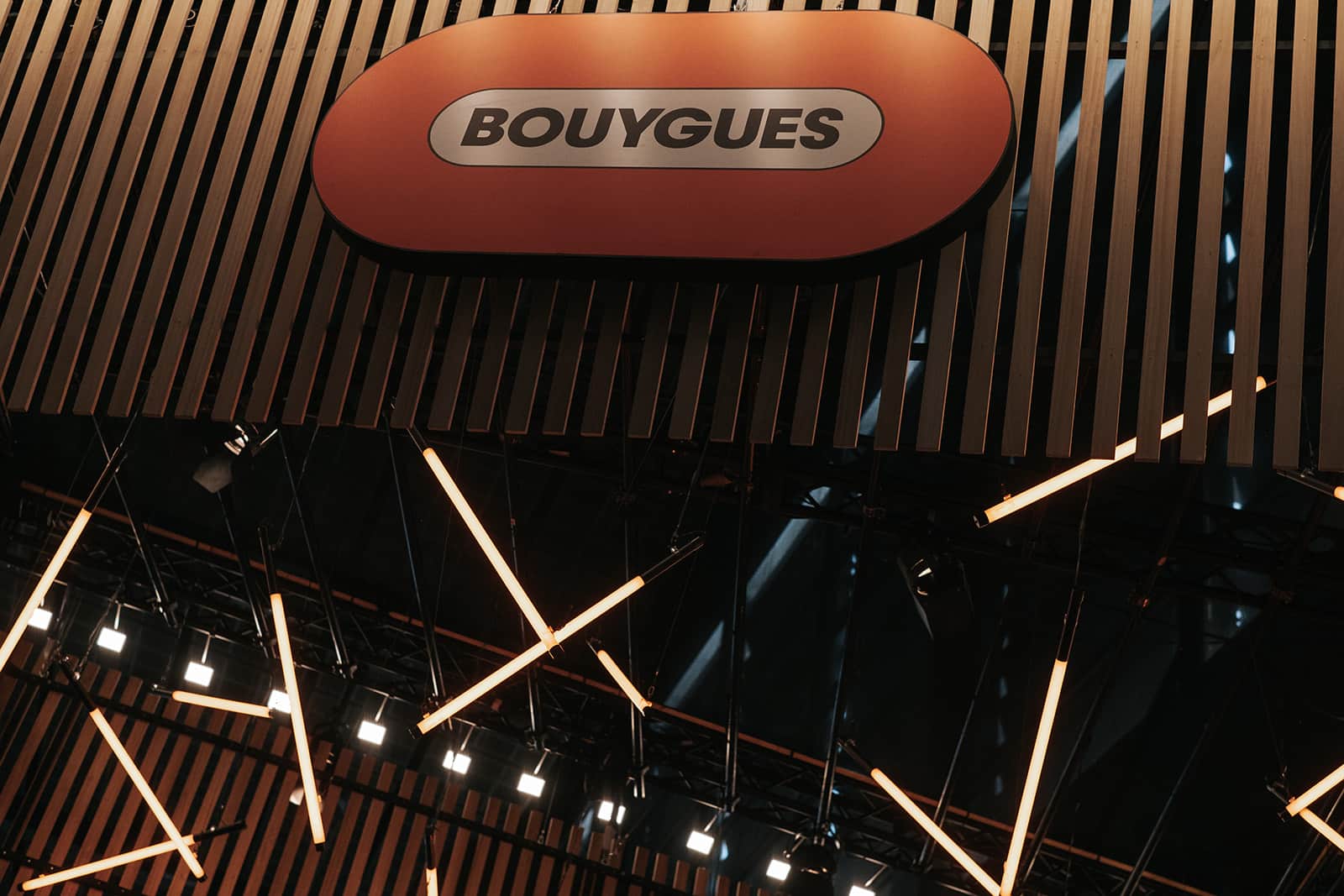